The senswork optical 2D metrology system ensures the correct feeding of microchips in the semiconductor industry. Discover the benefits.
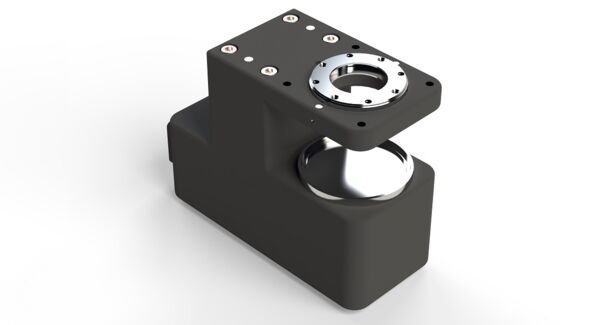
Pick & Place for Robotic Systems
Precise solutions for position recognition
The position detection and guidance of parts has several purposes:
Based on standardized industrial interfaces, our reliable systems are compatible with all common robot manufacturers in the industry.
The position detection of products by means of image processing is essential for automated gripping and joining processes. Often, purely mechanical feeding of components is not sufficient if they have to be gripped or joined precisely. Only sensibly designed high-resolution camera systems and suitable calibration methods can compensate for inaccuracies in the feed and prevent damage during the gripping process or assembly.
Calibration makes it possible to determine the exact spatial relationship between the camera coordinate system and the robot coordinate system. This allows the captured visual information to be correctly matched to the robot's movements, ensuring precise positioning and gripping is achieved.
For conveyor tracking tasks, senswork offers additional modules for the detection of moving workpiece carriers and position adjustment with the controller. Accuracies < 0.1 mm in position and orientation can be achieved through precise time alignment.
The senswork optical 2D metrology system ensures the correct feeding of microchips in the semiconductor industry. Discover the benefits.
A high-precision camera system from senswork secures the joining process of glass and display in a hybrid bonding system.
Capture the position and location of welding spoons with transmitted light illumination from senswork. Reliable and precise.
Rainer Obergrussberger
CEO
Business Development
senswork GmbH
Gewerbepark Lindach D 3
84489 Burghausen
Contact us.