Quality Assurance for Industrial Automation
Machine Vision Systems from a One-Stop Shop
Our Passion
We develop custom-fit machine vision solutions for complex quality assurance tasks - efficient, precise, and innovative
Our Offer
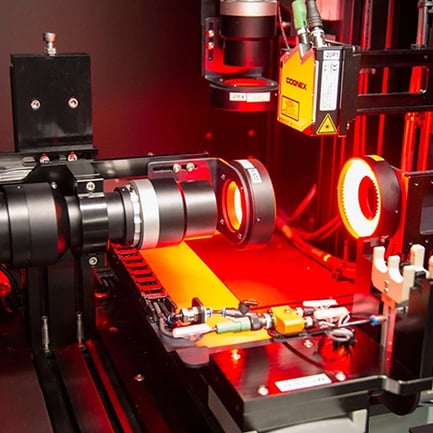
Optical Measuring & Testing Technology
Sophisticated Methods
Optical Measuring & Testing Technology
Sophisticated Methods
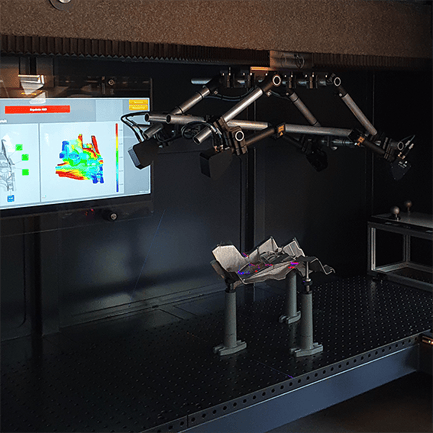
Solutions
Successful Applications
Solutions
Successful Applications
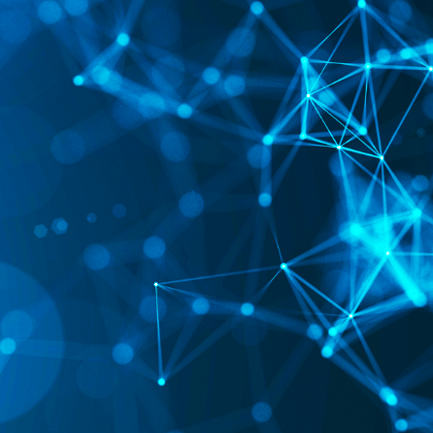
Products
Vision Software & Hardware
Products
Vision Software & Hardware
State-of-the-art image processing: senswork AI in optical inspection
3D acquisition of shape, position & surface
To ensure flawless surfaces
Final product inspection
Pick & Place for robotic systems
Optical 3D Inline Measurement Replaces CMM
Testing of printed or embossed symbols, text, codes on a wide variety of surfaces
Measure, inspect and avoid errors in 2D
The Right Technology
At the beginning of a project, we select the right measurement and inspection technology for your specific application. Based on this, we develop your customized vision system. Our solutions automate measurement and inspection processes, resulting in a fast return on investment. They also save you time, resources and space. In addition, our technologies help reduce scrap in manufacturing processes. We place great emphasis on high precision, reliability and the optimization of your processes.
All designs of our measuring and testing systems are created in the design department. Precisely tailored to your requirements.
Our software architects are constantly developing the software applications, so that your products are reliably tested.
Our turnkey measuring and testing systems are created in our workshop. They also undergo tests here before they are delivered.
Our support team accompanies you throughout the entire project until commissioning. Even after completion of a project, we are there for you.
Our Expertise
From initial concept to commissioning - our multidisciplinary team manufactures machine vision systems in-house
References
-
Wolfgang Gmach Siltronic AG We value senswork as a reliable partner when it comes to camera-based solutions. We use the systems, which were developed specifically for us with a high level of customer orientation, at all of our production sites globally."
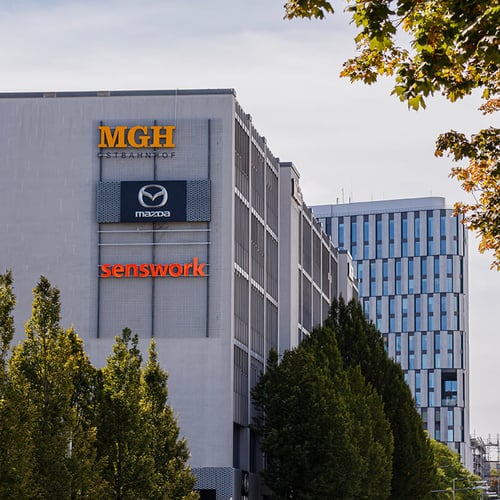
senswork Innovation Lab
In the Munich Innovation Lab, we develop new approaches to solutions with AI
We capture new findings and technologies for industrial image processing at an early stage in order to make them usable in industry and research. In the senswork Innovation Lab, we dedicate ourselves specifically to AI technology Deep Learning, which offers new possibilities for demanding inspection tasks in image data analysis and thus in automated production processes. In this way, we are paving the way for the future of quality assurance in the machine vision industry.
Do you need a solution for automated optical measurement or inspection? Don't hesitate to contact us. Send us a short description of your inspection task, the manufacturing environment and information about the object. Our team of experts will be happy to assist you!
Highlights
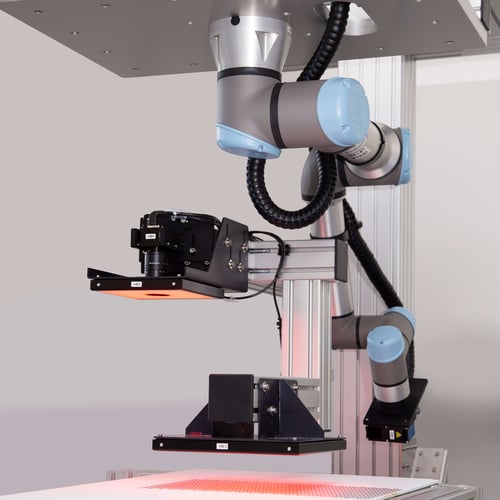
Camera guided robotics
senswork & Robotic Vision
Robots are a useful helper - not only for gripping components, but also for aligning cameras or 3D sensors to different inspection areas of a component. We offer optical measurement and inspection systems in combination with collaborative robots.
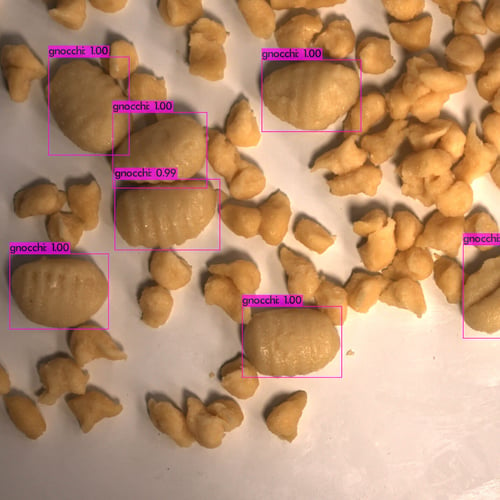
Optimizing processes with AI
senswork Neuralyze® Vision AI
Pasta products such as gnocchi and spaetzle are produced in a very similar way. When production is switched from one manufacturing process to another, it is important to ensure that the pasta is packaged according to type. Visual inspection using deep learning helps distinguish between them. Find out how AI technology is improving the process and the expertise behind it.
Company brochure
Learn more about senswork
Our company brochure provides a brief overview of our competencies, product portfolio and services in the field of machine vision.
.png?width=700&height=500&name=senswork-brochure-w(1).png)
We are committed to sustainable development and act responsibly because we believe in what we do. And we lead by example, treating our employees with respect and supporting their professional growth and development. It also goes without saying that we use resources wisely and that our products are safe and efficient.