Das optische 2D-Messsystem von senswork sorgt für die korrekte Zuführung von Mikrochips in der Halbleiterindustrie. Entdecken Sie die Vorteile.
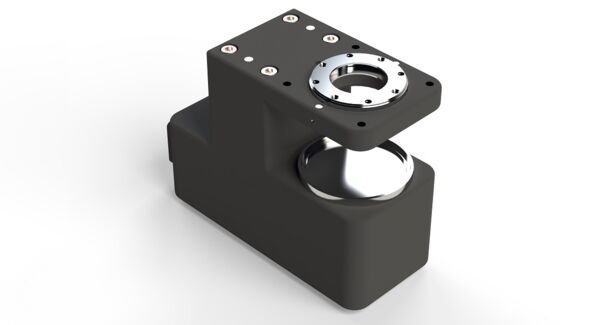
Pick & Place für Roboteranlagen
Präzise Lösungen für die Lageerkennung
Die Lageerkennung und Führung von Teilen hat verschiedene Zwecke:
Basierend auf standardisierten Industrieschnittstellen sind unsere zuverlässigen Systeme zu allen gängigen Roboterherstellern in der Industrie kompatibel.
Die Positionserkennung von Produkten mittels Bildverarbeitung ist für automatisierte Greif- und Fügeprozesse unerlässlich. Oft reicht eine rein mechanische Zuführung von Komponenten nicht aus, wenn diese präzise gegriffen oder gefügt werden müssen. Erst durch sinnvoll ausgelegte hochauflösende Kamerasysteme und geeignete Kalibriermethoden können Ungenauigkeiten in der Zuführung ausgeglichen, und Beschädigungen beim Greifprozess oder in der Montage vermieden werden.
Die Kalibrierung ermöglicht es, die genaue räumliche Beziehung zwischen dem Kamerakoordinatensystem und dem Roboterkoordinatensystem zu ermitteln. Dadurch können die erfassten visuellen Informationen korrekt auf die Bewegungen des Roboters abgestimmt werden, was eine präzise Positionierung und Greifoperation gewährleistet.
Für Conveyor-Tracking-Aufgaben bietet senswork zusätzliche Module zur Erfassung von bewegten Werkstückträgern und dem Positionsabgleich mit der Steuerung. Durch einen präzisen zeitlichen Abgleich können Genauigkeiten < 0,1 mm in Position und Lage erzielt werden.
Das optische 2D-Messsystem von senswork sorgt für die korrekte Zuführung von Mikrochips in der Halbleiterindustrie. Entdecken Sie die Vorteile.
Ein hochgenaues Kamerasystem von senswork sichert den Fügeprozess von Glas und Display in einer Hybrid-Bonding-Anlage.
Erfassen Sie die Position und die Lage von Schweißlöffeln mit Durchlichtbeleuchtung von senswork. Zuverlässig und präzise.
Rainer Obergrussberger
Geschäftsführer
Business Development
senswork GmbH
Gewerbepark Lindach D 3
84489 Burghausen
Kontaktieren Sie uns! Rufen Sie an oder hinterlassen Sie eine Nachricht.